HVAC AUTO DUCT LINE II
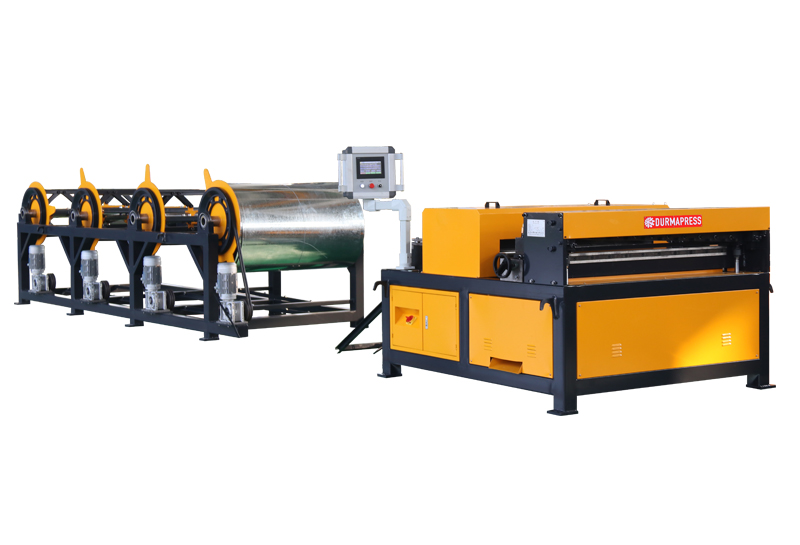
DUCT AUTO LINE II
Duct production line 2 can drive blanking for duct and TDF flange forming machine at the same time.Combined with TDF flange forming machine, rolling reel machine, crimping machine and relevant comer code, duct production line 2 can produce high-quality products.
Basic Information
HVAC Rectangular Duct line Square duct Auto Prodution Line II for Square Duct Forming Making
HVAC duct machine Working Schematic Diagram:
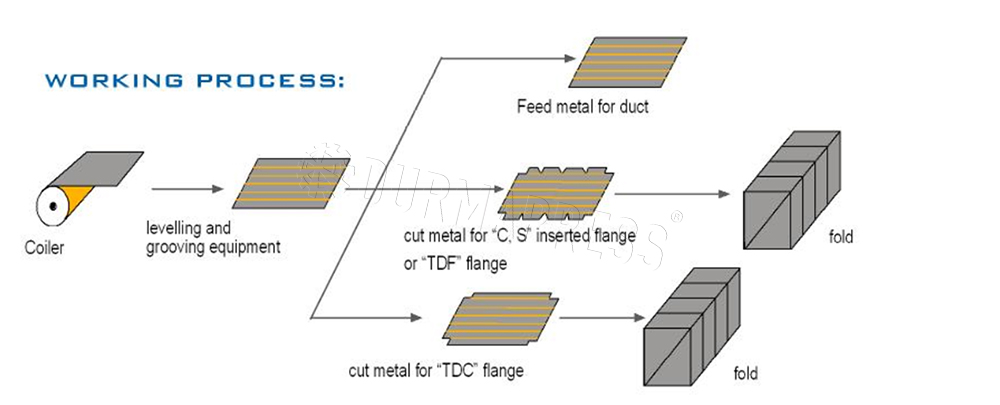
I. Advantage of Products:
The auto duct production line 2 machine can be used to feed material for HVAC duct manufacturer. Meanwhile, it can feed sheet metal for TDF flange. The functions mainly include leveling, grooving, notching, and cutting.
This machine can be used with TDF flange forming machine, Pittsburgh lock forming machine, folding machine, and corner machine together. Adopted aluminum alloy suspension arm, the machine is more easy to operate.
The built-in control cabinet reduces wiring as the whole structure and makes it convenient to move. Imported configuration is very stable and convenient to use. The imported equipment includes Japan Mitsubishi CNC system, Schneider electrical system, Beijing Huade and Taiwan hydraulic system and Japan Omron encoder. Besides, basic configuration includes one electric coil rack 2 material trays, a set of leveling and beading equipment, the hydraulic angle-notching machine with four sets of molds, hydraulic shearing machine and a set of CNC control system and software.
We can also provide customers 2 material racks (4 material coil) in accordance with different requirements. We have both CNC HVAC duct production line which can make ventilation air duct automatically and separate machines which are easier to move and more convenient to operate. For the auto duct line 2 machine, it’s very easy to operate because it’s usually used to finish leveling, beading, notching and shearing 4 steps.
But the machine is also suitable for upgrading to auto duct line 4 and auto duct line 5 in the future. It will be more saving cost, improving efficiency and saving labor. About after-sales service, we have professional technicians who can teach you how to operate machines by video and we can also provide engineer overseas service or you can send your workers to our factory in China to learn operation method.
II. Function:
1.Electric decoilers (2 sets of rollers) driven by independent frequency controlled motors.
2.Multi-functional main body with capability of leveling,beading, notching(capable of sharp notching, TDF notching) and plate shearing.
3.Mitsubishi computer controlling system and software.
4.Mitsubishi and Siemens electric box and electrics.
III. Main lmport Configuration:
- Japan Mitsubishi CNC control system+Schneider electrical system
- Beijing Huade or hydraulic system from Taiwan
- Japan Omron encoder
IV.Basic Configuration:
- One electric coil cradle (two material trays)
- One set leveling and beading equipment
- Hydraulic angle-shearing machine with four sets of die
- Hydraulic sheet-shearing machine
- A set of CNC computer control system and production software
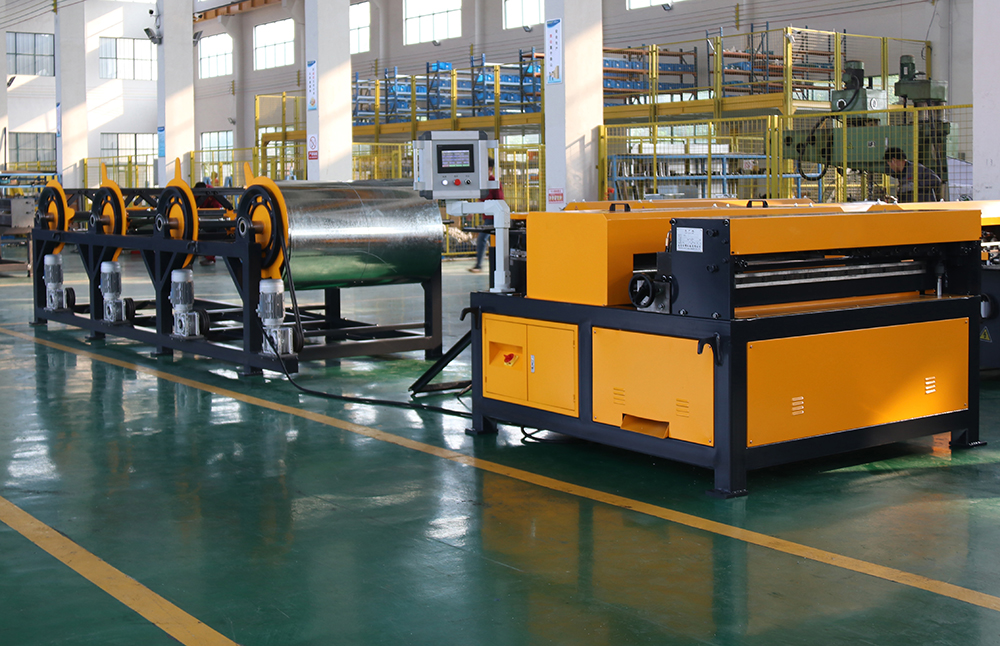
Machine Frame
The machine frame adopts welding square steel,annealing treatment and overall processing toensure the stability and flatness of the frame and processing accuracy
PLC Control
Use Germany Siemens PLC controller whichcan accurately control the machining length,particularly suitable for production of ”L” and”口“-
shaped pipe with different size.
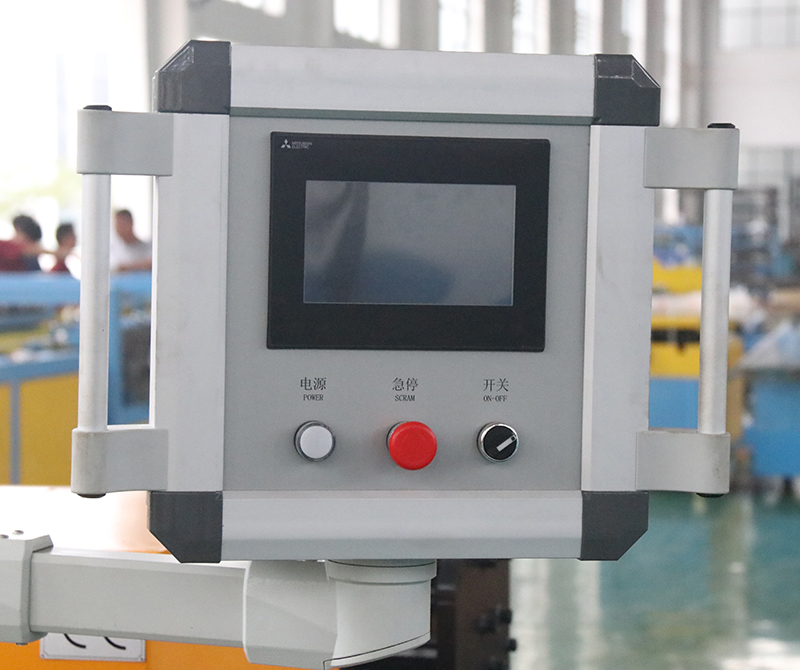
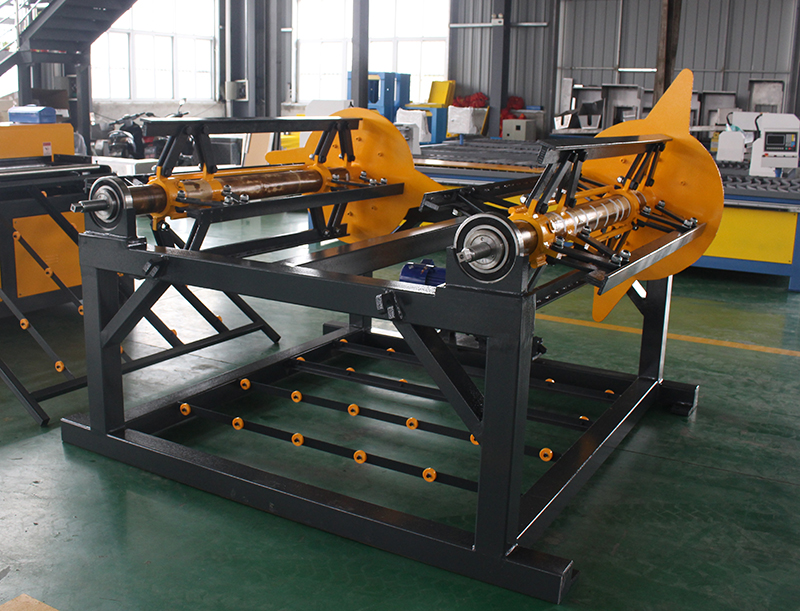
Decoilers
Double coilers with adjustable coiling diameterof 500-600mm, loading capacity of each coilerreaches to 7T, driven by high-performancemotor and reducer, which significantly improve
the practicability of coiler.
Loading Feeder
The upper loading feeder is supported withrubber bearing to prevent plate surface fromscratching, and right and left sides are equipped
with adjustable supporting arms.
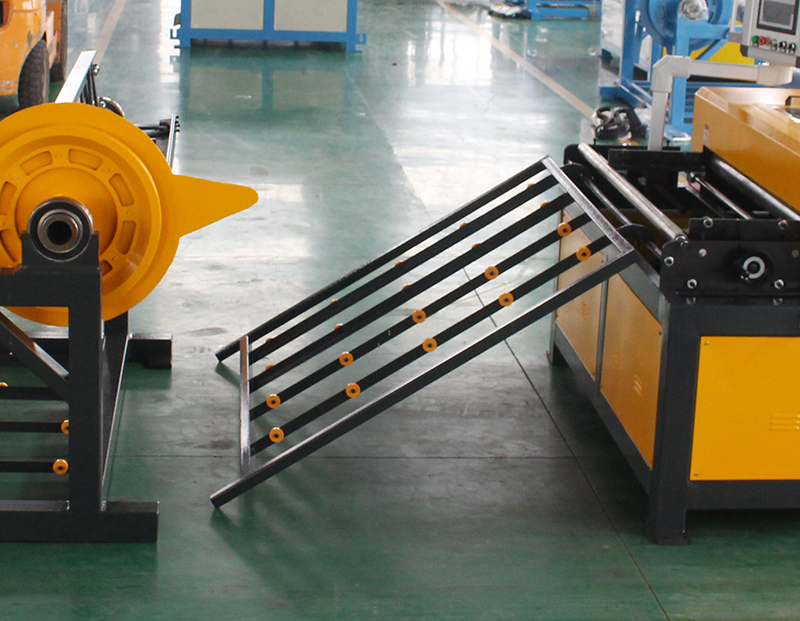
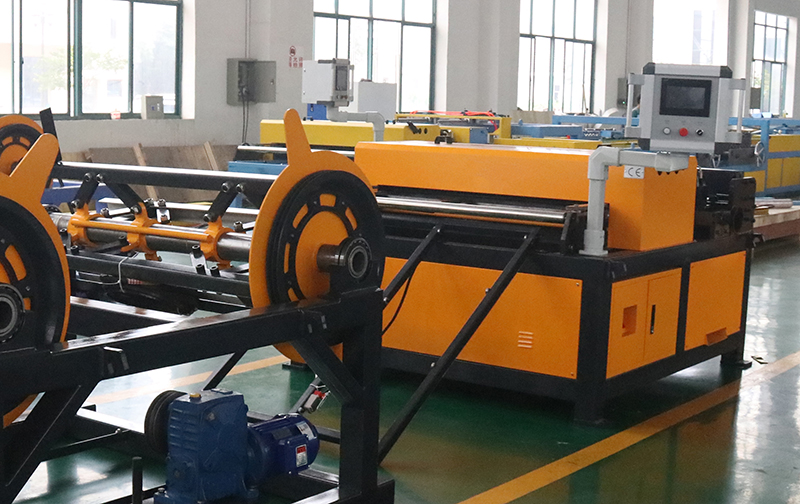
Feeding Inlet
The feeding inlet is provided with a secondaryfeeding guiding rack to ensure feeding accuracy
and improve its property against deviation
Rollers
Use 2 feeding rollers, 4 leveling rollers, 2 beadingrollers, all made by 45# quenched and tempered steel through fine grinding, chrome-coatedtreatment to ensure the roller strength andservice life. beading slope distance is 210mm,driven by inverter motor, through Omron encodertransmitting signals to ensure the feeding stability.
Bevel gear and spur gears are made bySAE8620H material to reduce wear and improve the gear life span.
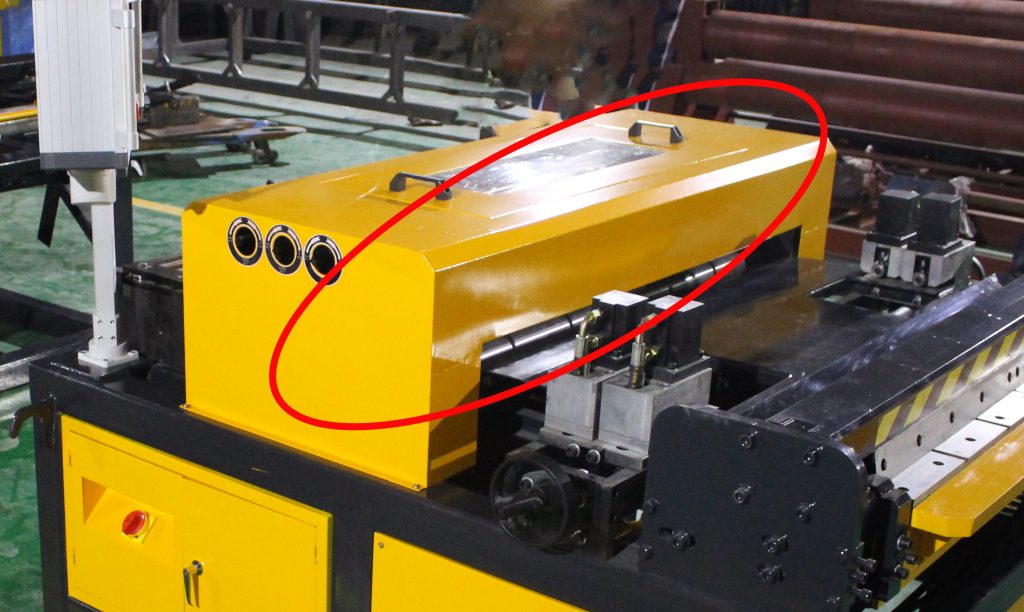
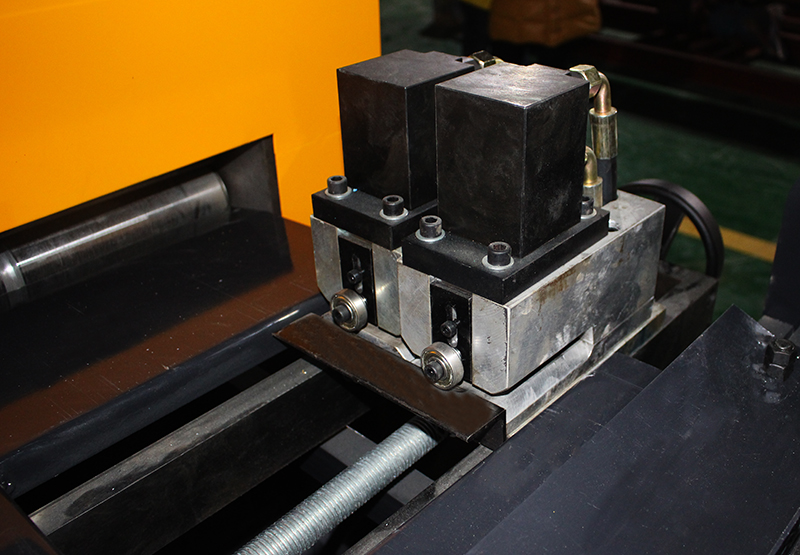
Angle notching
Notching”V””口”groove, the dies are made byCr12Mov material with longer service life. Cuttingangle and depth are adjustable, convenience for
production.
Sheet Cutting
Cutting method: holding-down on up side,hydraulic transmission, the blade is made by 6CrW2Si steel that can cutting stainless steel,
cutting thickness within 0.5-1.2mm.
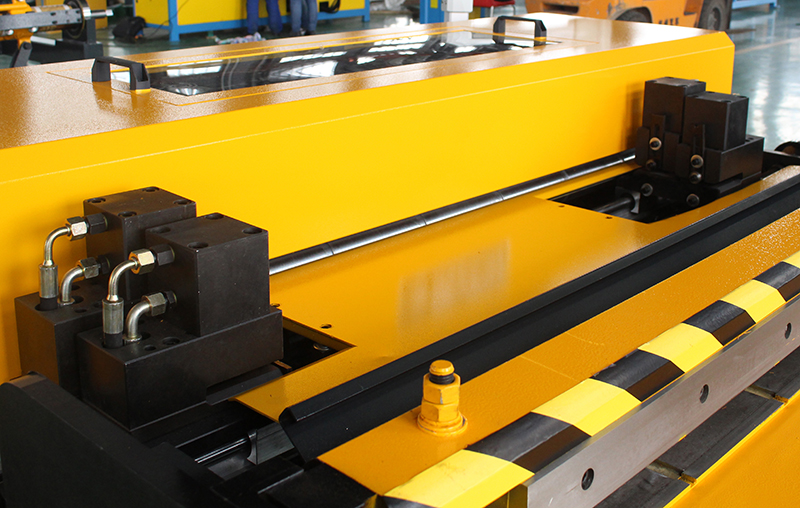
TECHNICAL DATA
Model | Sheeting Thickness(mm) | Max Width(mm) | Max working speed(m/min) | Max weight of sending coil | Dimensions(L*W*H ) | Power(KW) | Weight(T) |
---|---|---|---|---|---|---|---|
DM2-1300 | 0.5-1.2 | 1300 | 15 | 7 | 1900*1950*1500 2500*1950*1600 | 7 | 3 |
DM2-1500 | 0.5-1.2 | 1500 | 15 | 7 | 1900*2150*1500 2500*2150*1600 | 8.5 | 3.2 |
Frequently Asked Questions
- You can choose the shipping company on your own. Or use our forwarder, we will quote you the CIF price.
- If less than one container,we will choose LCL (less container load), it will be cost-efficiency. If you purchase two and above, we will use 20″, 40″ or HQ container according to the machines size.
Durmahvac is a mature brand in China. We have CE, ISO and SGS certification to prove our quality. We welcome your visit, seeing is believing.
- T/T (30% advance payment, and 70% balance paid one week before shipment)
- L/C (100% L/C at sight), this should be negotiated first.
We always prepare stock for our clients. Contact us to learn more details.
Normally 15 days.